Die Jahre 2015 und 2016 könnten als der Wendepunkt für den Direktmetalldruck (Direct Metal Printing; DMP) innerhalb der Luft- und Raumfahrtindustrie betrachtet werden, da die Technologie zunehmend den Schritt vom Prototypenbau zu flugfertigen Teilen und Baugruppen ermöglichte.
Die Zusammenarbeit zwischen Airbus Defence and Space und 3D Systems führte in dieser Phase zu einem entscheidenden Durchbruch: Der erste 3D-gedruckte Hochfrequenzfilter wurde getestet und für den Einsatz in kommerziellen Telekommunikationssatelliten validiert. Das Projekt stützte sich auf Forschungsarbeiten, die von der European Space Agency finanziert wurden (A0/1-6776/11/NL/GLC: Modelling and Design of Optimised Waveguide Components Utilising 3D Manufacturing Techniques).
HF- oder Hohlleiterfilter aus Metall gehen auf die ersten Weltraumkommunikationssysteme vor fast 50 Jahren zurück. Sie funktionieren wie Verkehrspolizisten, die bestimmte Frequenzen auf ausgewählten Kanälen durchlassen und Signale außerhalb dieser Kanäle abweisen.
Ein wichtiger Branchentrend ist die Erhöhung der Kapazität für mehrere Beams innerhalb eines einzigen Satelliten. Ein Hochleistungssatellit wie der von Airbus Defence and Space hergestellte Eutelstat KA-SAT birgt fast 500 HF-Filter und mehr als 600 Wellenleiter. Viele davon sind speziell für die Handhabung bestimmter Frequenzen entwickelt worden.
Kritische Anforderungen erfüllen
Telekommunikationssatelliten sind ein Beispiel dafür, dass die Luft- und Raumfahrtindustrie unermüdlich auf Gewichtsreduzierung setzt – ein Objekt in eine geostationäre Umlaufbahn zu schicken, kann bis zu 20.000 $ pro Kilogramm kosten. Die kontinuierliche Verbesserung des Designs und eine verkürzte Produktionszeit sind ebenfalls wichtige Prioritäten, da die meisten Satelliten für eine Lebensdauer von 10–15 Jahren ausgelegt sind.
Diese Prioritäten machen Telekommunikationssatelliten zum idealen Kandidaten für den Direktmetalldruck. Mit dem im Airbus-HF-Filterprojekt verwendeten ProX® DMP 320 von 3D Systems können Hersteller folgende Vorteile erzielen: Zusammenführung von Teilen; Verbesserung der Funktionalität durch Formen und Oberflächen, die mit herkömmlichen Mitteln nicht hergestellt werden können; Verkürzung der Produktionszeit sowie Senkung der Kosten für kundenspezifische Designs; Reduzierung des Gewichts unter Beibehaltung oder Verbesserung der Materialfestigkeit.
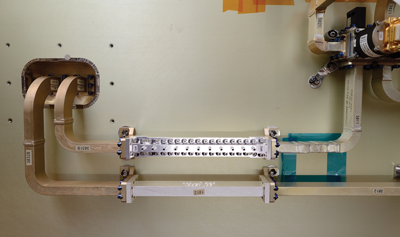
Neue Anwendung für bewährten Drucker
Die Einrichtung von 3D Systems in Leuven, Belgien, verwendet den ProX DMP 320 von 3D Systems bereits seit der Zeit, in der sich die Maschine in der Beta-Phase befand. Zu den erfolgreichen Projekten gehören die topologische Optimierung, die Gewichtsreduzierung und die Zusammenführung von Teilen, die für die Raumfahrt validiert werden, z. B. Halterungen und Endstücke für die Montage von Verstrebungen bei Telekommunikationssatelliten. Das Projekt Airbus Defence and Space war für 3D Systems Leuven der erste Ausflug in die Welt der HF-Filter.
Der ProX DMP 320 ist für hohe Präzision und hohen Durchsatz in anspruchsvollen 24/7-Produktionsumgebungen ausgelegt. Die breite Palette an LaserForm-Legierungen (Titan, Edelstahl, Aluminium, Nickel-Chrom- und Kobalt-Chromstahl) wurde genau für diesen Metalldrucker entwickelt, um eine hohe Teilequalität und gleichbleibende Eigenschaften zu gewährleisten.
Auswechselbare Fertigungsmodule bieten eine größere Anwendungsvielfalt und weniger Ausfallzeiten beim Wechsel zwischen verschiedenen Teilematerialien. Eine kontrollierte Vakuumkammer für den Build stellt sicher, dass jedes Teil mit nachweisbaren Materialeigenschaften, Dichte und chemischer Reinheit gedruckt wird.
Bahnbrechende Designinnovation
Das RF-Filter-Projekt von Airbus Defence and Space zeigt, wie mit dem 3D-Druck innovative Designs für Luft- und Raumfahrtbauteile entwickelt werden können, die sich seit Jahrzehnten nicht wesentlich verändert haben.
HF-Filter werden herkömmlicherweise auf der Grundlage von Bibliotheken mit standardisierten Elementen entworfen, wie z. B. rechteckige Kavitäten und Hohlleiterquerschnitte mit rechtwinkligen Verläufen. Formen und Verbindungen werden durch typische Fertigungsverfahren wie Fräsen und Funkenerosion vorgegeben. Infolgedessen müssen Kavitäten für HF-Filter in der Regel aus zwei bearbeiteten und dann miteinander verschraubten Hälften hergestellt werden. Dies führt zu einem höheren Gewicht, verlängert die Produktionszeit um einen Montageschritt und erfordert eine zusätzliche
Qualitätsbewertung.
Die Konstruktion der Teile für den 3D-Druck ermöglichte es Airbus Defence and Space, komplexe Geometrien ohne zusätzliche Herstellungskosten zu untersuchen.
CST MWS, ein 3D-Standardsoftwaretool für elektromagnetische Simulationen, wurde für den Entwurf der 3D-gedruckten HF-Filter verwendet, wobei nur wenig Zeit für die Optimierung erforderlich war. Die höhere Flexibilität in der Fertigung, die durch den 3D-Druck möglich wurde, führte zu einem Design mit einem vertieften super-elliptischen Hohlraum. Die einzigartige Formgebung trug dazu bei, HF-Ströme zu kanalisieren und die erforderlichen Kompromisse zwischen dem Q-Faktor – einem Maß für die Effizienz eines Wellenleiters durch Beurteilung von Energieverlusten – und der Unterdrückung von
Signalen außerhalb des gewünschten Bandes zu schließen.
„Die bahnbrechende Neuerung liegt darin, dass nun die reine Funktionalität, nicht die Herstellbarkeit, das Design der Hardware bestimmt“, sagt Koen Huybrechts, Projektingenieur bei 3D Systems in Leuven. „Dieses Projekt ist ein klassisches Beispiel für ,form follows function’.“
„Die wichtigsten Vorteile einer monolithischen Konstruktion, die durch den 3D-Druck ermöglicht wird, sind Masse, Kosten und Zeit“, sagt Paul Booth, HF-Ingenieur für Airbus Defence and Space in Stevenage, Großbritannien. „Die Masse wird reduziert, weil keine Befestigungsmittel mehr erforderlich sind. Außerdem folgt das Außenprofil besser dem Innenprofil – ein kostenloser Bonus des Direktmetalldrucks. Auf diese Weise wird nur so viel Metall wie gerade notwendig verbraucht. Der Kosten-/Zeitvorteil ergibt sich aus der Reduzierung in der Montage und der Nachbearbeitung.“
Beseitigen von Oberflächenproblemen
Ursprünglich wurde die unterschiedliche Oberflächentopologie in 3D-gedruckten Metallteilen als Problem angesehen, aber umfangreiche Tests durch Airbus Defence and Space konnten diese Bedenken ausräumen.
„Die mikroskopische Topologie ist im 3D-gedruckten Teil anders als in einem gefrästen Teil“, sagt Booth. "Gefräste Oberflächen haben scharfe Spitzen und Täler, während die 3D-gedruckte Oberfläche aus verschmolzenen Sphäroiden besteht, sodass die Schärfe weniger stark ist.
„Die Kugelform der im 3D-Metalldruck verwendeten Pulverpartikel führt zu einer gewissen Welligkeit statt harter Übergänge“, sagt Huybrechts, „aber die Möglichkeit, ein Teil gemäß einer effektiveren Signalfilterung zu formen, beseitigt jegliche Bedenken hinsichtlich der Beschaffenheit der Oberflächen."
„Wir waren sehr zufrieden mit der Arbeit, die 3D Systems für uns geleistet hat, und viele Mitarbeiter von Airbus haben sich dazu geäußert, wie gut die Oberflächenbeschaffenheit ist“, sagt Booth. „Wir haben einige Röntgen-CT-Scans durchgeführt und waren von der Dichte des Teils und dem allgemeinen Oberflächenfinish beeindruckt.“
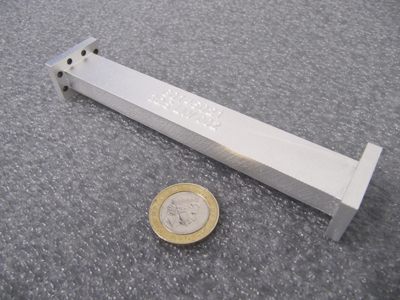
Strenge Tests bestehen
Drei Aluminiumproben, die auf dem ProX DMP 320 unter Verwendung unterschiedlicher Verarbeitungswege gedruckt wurden, wurden von Airbus Defence and Space am Standort in Stevenage getestet. Die Tests ahmten die Bedingungen nach, denen die Teile während des Starts und im Orbit ausgesetzt wären, einschließlich Vibrationen, Stößen und thermischen Belastungen wie extremen Temperaturen und Bedingungen im Vakuum. Alle drei Proben erfüllten oder übertrafen die Anforderungen, wobei die beste Leistung von einem Filter kam, der in einem elektrolytischen Verfahren silberbeschichtet wurde.
Über den 3D-Druck hinaus lieferte 3D Systems einen Mehrwert, der für diese Art von Projekt entscheidend ist, darunter die zertifizierte Pulververarbeitung, Prozesssteuerung für überlegene Materialdichte, bewährte Nachbearbeitung und zuverlässige Qualitätskontrolle.
Booth räumt ein, dass dieses zusätzliche Fachwissen eine Schlüsselrolle für den Erfolg des Projekts gespielt hat: „Wir wissen, dass nicht nur die Nutzung einer guten Maschine für die Herstellung des Teils, sondern auch die Kenntnisse von 3D Systems in Bezug auf den Herstellungsprozess zum Erfolg beigetragen haben.“
Riesiges ROI-Potenzial
Jetzt, da der Prozess validiert ist und die Teile den höchsten Raumfahrtnormen von Airbus Defence and Space entsprechen, kann das Unternehmen damit beginnen, das Renditepotenzial für den 3D-Metalldruck zu prüfen. Das Projekt lieferte eine Kapitalrendite, die jeden CFO begeistert: schnellere Durchlaufzeiten, reduzierte Produktionskosten und eine erstaunliche Gewichtsreduzierung von 50 Prozent.
„Die Masse wurde reduziert, ohne Zeit für die Optimierung aufzuwenden“, sagt Booth, „und sie kann durch radikaleres mechanisches Design weiter reduziert werden. Die geringere Masse spart Kosten, da weniger Treibstoff in der Rakete benötigt wird und weniger Anforderungen an die Stützstrukturen gestellt werden, was eine weitere Massenreduzierung ermöglicht.
„Der Erfolg dieses Projekts eröffnet die Möglichkeit für eine viel stärkere Integration von HF-Filtern mit mechanischen und thermischen Komponenten, um die Anzahl der Teile und die Gesamtmasse zu reduzieren. Wir werden uns auch mit der Integration weiterer Funktionen befassen, wie z. B. Testkoppler als Teil des Filters oder direkt integriert in die Wellenleiter-Verläufe. Es gibt ein enormes Potenzial für die Reduzierung der Masse bei gleichzeitiger Reduzierung der Produktionszeit und ‑kosten.“